The Ultimate Guide to CNC Machine Suppliers in the Metal Fabrication Industry
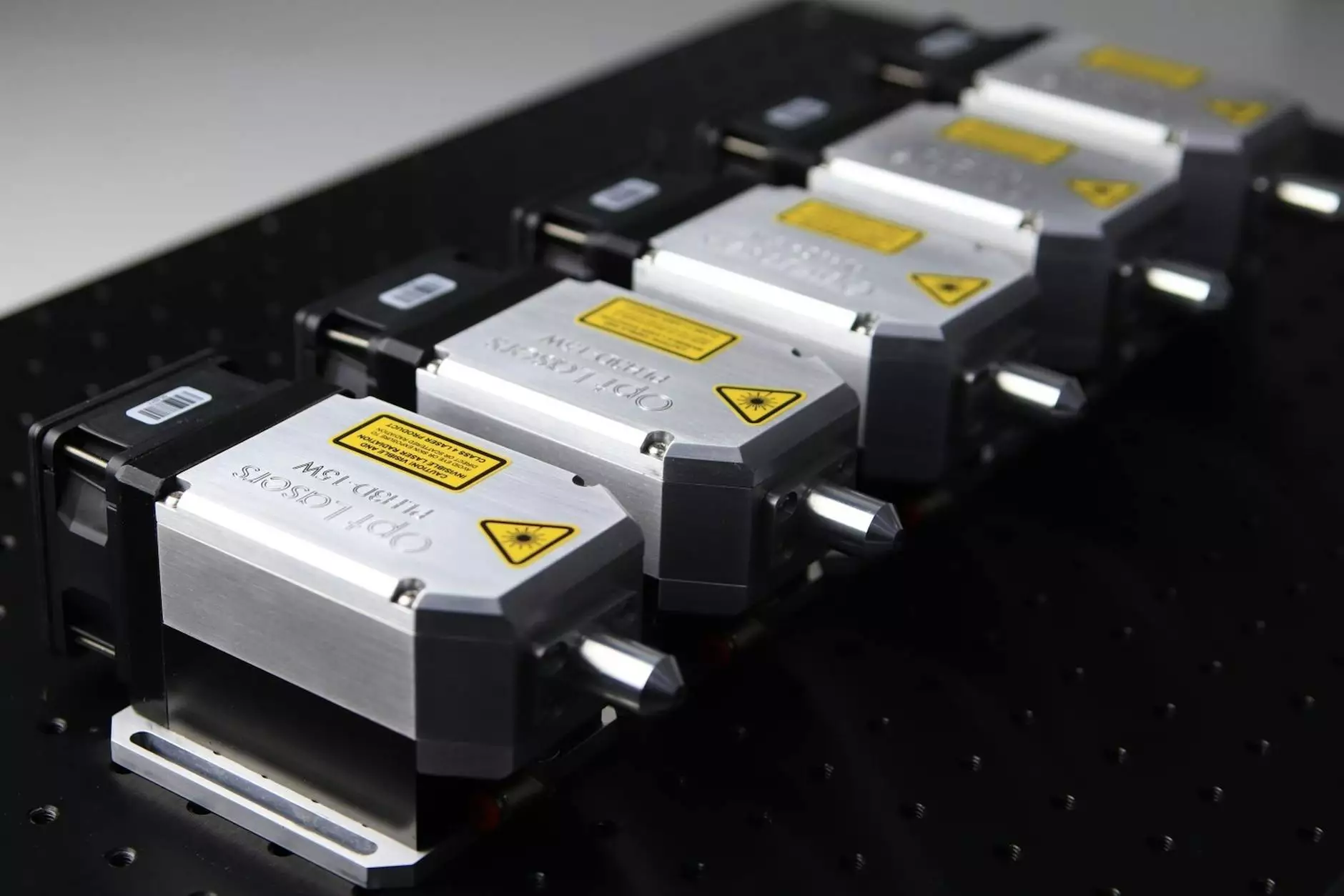
In today's fast-paced manufacturing landscape, CNC machine suppliers hold a crucial position, particularly within the metal fabrication sector. The precise and advanced technology of CNC (Computer Numerical Control) machining allows businesses to enhance productivity, reduce waste, and achieve exemplary precision. In this comprehensive guide, we will delve deeper into what CNC machines are, the importance of CNC machine suppliers, and how to choose the right supplier for your business needs. We will also explore the different types of CNC machines available and their applications in metal fabrication.
What is CNC Machining?
CNC machining is a manufacturing process that utilizes computer software to control machine tools. This technology can create complex shapes and components with high precision and minimal human intervention. CNC machines are widely used in various industries, including automotive, aerospace, and medical, enabled by their ability to perform tasks such as:
- Cutting: CNC machines can precisely cut materials into specific shapes and sizes.
- Milling: They can mill surfaces to achieve smooth finishes or intricate designs.
- Turning: CNC lathes can produce cylindrical parts with excellent accuracy.
- Drilling: Drilling holes in various materials is easily accomplished with CNC machines.
The Importance of CNC Machine Suppliers
CNC machine suppliers are integral partners for businesses engaged in metal fabrication. Their role transcends merely providing machines; they offer a range of services and support that enhances the operational efficiency of manufacturing processes. Here are several key aspects:
1. Diverse Range of Equipment
One of the primary advantages of working with CNC machine suppliers is access to a diverse range of machinery and tools. Suppliers offer:
- Milling Machines: For a wide array of milling applications.
- Turning Centers: Ideal for producing symmetrical precision parts.
- Laser Cutters: For intricate designs and high-speed operations.
- Plasma Cutters: Suitable for thick materials.
2. Technical Expertise
Purchasing a CNC machine is a significant investment. Reputable CNC machine suppliers offer extensive technical knowledge, assisting businesses in selecting the most suitable machine for their needs.
3. After-Sales Support
Having access to reliable after-sales support is vital in the manufacturing industry. Suppliers typically provide:
- Training Programs: To ensure operators are well-equipped to use the machines.
- Maintenance Services: Regular upkeep to prevent downtime and costly repairs.
- Technical Assistance: For troubleshooting and optimizing machine performance.
Choosing the Right CNC Machine Supplier
When it comes to selecting a CNC machine supplier, several factors must be taken into consideration to ensure that your investment meets your business needs:
1. Evaluate Reputation and Experience
Start by examining the supplier's reputation in the industry. Look for:
- Client Testimonials: Previous customers can provide insights into their experiences with the supplier.
- Industry Awards: Recognition from industry peers can indicate reliability and quality.
- Years of Experience: A proven track record often correlates with expertise.
2. Range of Products
A good supplier should carry a comprehensive range of CNC machining equipment to cater to various manufacturing needs. This allows for scalability and flexibility in operations.
3. Price and Value
While cost is a significant factor, it’s crucial to assess the overall value offered by the supplier. This includes the quality of machines, available support, and after-sales services. Cheaper doesn’t always mean better—consider long-term costs and benefits.
4. Support and Training
Training and support are essential for maximizing the productivity of CNC machines. Choose suppliers that offer robust training programs and responsive support.
Types of CNC Machines Utilized in Metal Fabrication
Metal fabricators use several types of CNC machines to carry out various tasks with precision and efficiency:
1. CNC Milling Machines
CNC milling machines are versatile and capable of producing complex parts through the milling process. They utilize rotating cutter tools to remove material from a workpiece. Applications include:
- Creating molds and dies
- Producing prototypical parts
- General machining of components
2. CNC Turning Machines
CNC turning machines, such as lathes, are essentially used to create cylindrical parts by rotating the material against cutting tools. They are ideal for:
- Manufacturing shafts and bearings
- Producing screws and fasteners
- Creating complex designs with consistent accuracy
3. CNC Laser Cutters
CNC laser cutters employ high-powered lasers to cut through materials with extreme precision. They are perfect for:
- Crafting intricate designs
- Cutting thin materials quickly
- Marking or engraving on various surfaces
4. CNC Plasma Cutters
CNC plasma cutters utilize plasma torches to cut through thicker materials, such as steel and aluminum, with high efficiency. Common applications include:
- Fabrication of components for machinery
- Cuts for automotive parts
- Creating artistic designs in metal
Benefits of Utilizing CNC Machines in Metal Fabrication
Incorporating CNC machining into metal fabrication offers numerous advantages, making it a popular choice for businesses:
1. Increased Precision
Precision is one of the most significant benefits of CNC machining. The reliance on computer controls reduces the margin for error, producing highly accurate components that meet stringent specifications.
2. Enhanced Productivity
CNC machines can operate continuously, performing tasks without the need for breaks. This capability enhances overall productivity and enables businesses to meet tight deadlines.
3. Versatile Applications
CNC machines can handle various tasks and processes. This versatility allows manufacturers to diversify their production capabilities without investing in multiple machines.
4. Reduced Waste
Advanced software and precise controls help minimize waste. This efficiency leads to cost savings and a reduced environmental impact.
5. Improved Safety
Automation of processes reduces the need for manual intervention, lowering the risk of accidents and injuries in the workplace.
Conclusion: Partnering with the Right CNC Machine Supplier
In conclusion, the role of CNC machine suppliers in the metal fabrication industry is invaluable. Understanding the importance of choosing the right supplier can vastly improve your production capabilities and drive your business toward success. From providing advanced machinery to offering comprehensive support and maintenance, a reliable supplier can make all the difference. As you contemplate your options, consider the factors we've discussed, and take the necessary steps to find a supplier that aligns with your operational goals. This partnership will not only enhance your production processes but also position your business at the forefront of the competitive manufacturing landscape. For further information and insights, visit deepmould.net.