Transforming Manufacturing Excellence: The Business of Plastic Moulding Electrical & Metal Fabricators
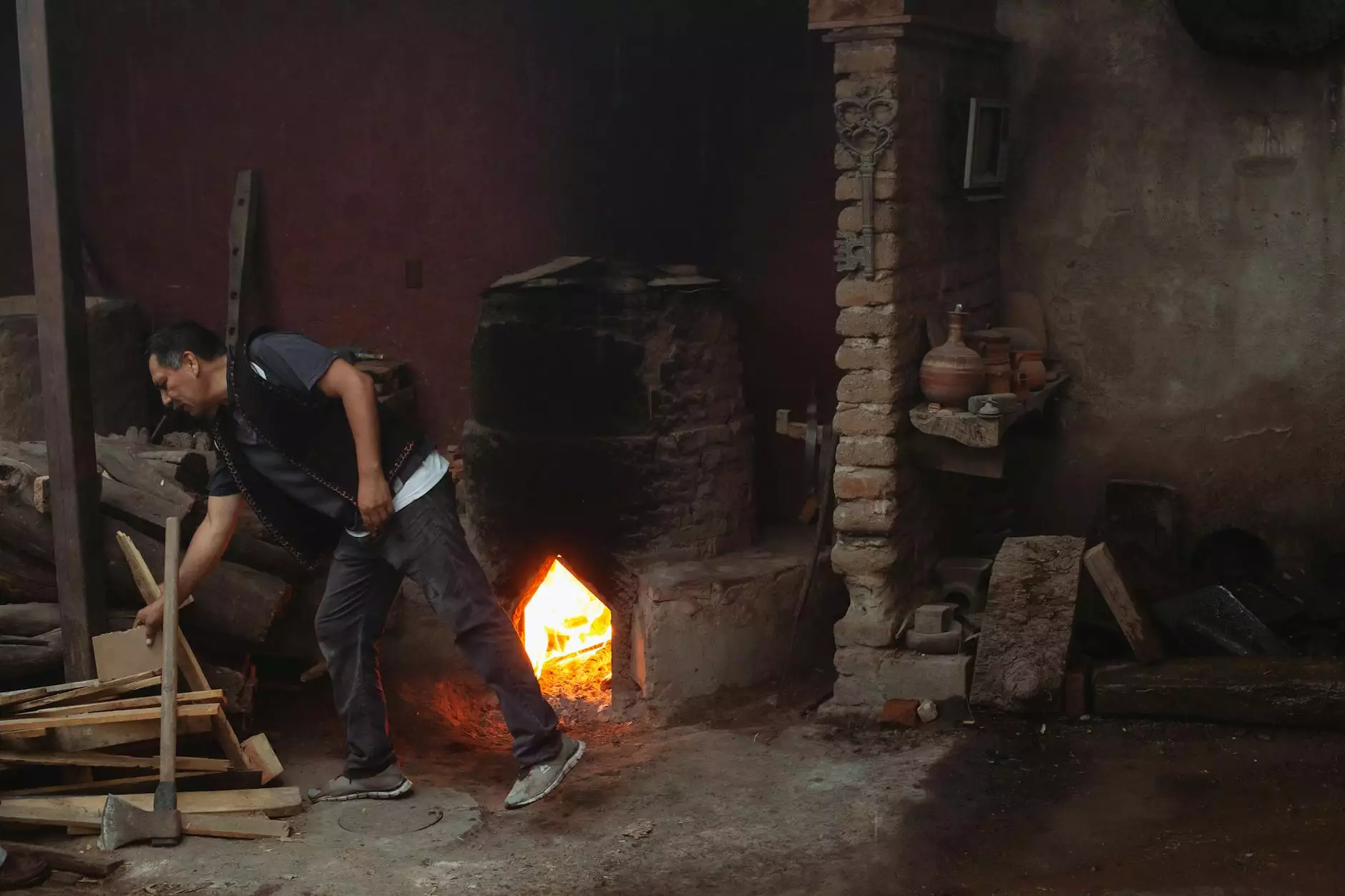
In today's dynamic industrial landscape, businesses engaged in plastic moulding electrical and metal fabrication are at the forefront of innovation, quality, and efficiency. At DeepMould, we specialize in delivering cutting-edge solutions that empower manufacturers to excel in competitive markets. Our focus on integrating advanced technologies, sustainable practices, and customer-centric approaches positions us as a leader in this vital sector.
Understanding the Critical Role of Plastic Moulding Electrical in Modern Industry
Plastic moulding electrical is fundamental to the production of complex electronic components, enclosures, and intricate plastic parts used across diverse industries, including automotive, consumer electronics, healthcare, and industrial machinery. The integration of electrical functionalities within plastic moulding processes has significantly enhanced product capabilities, enabling smarter, more durable, and high-performance end-products.
The Evolution of Plastic Moulding Electrical
Traditionally, plastic moulding involved shaping plastic materials into desired forms using techniques such as injection moulding, blow moulding, and compression moulding. With the advent of plastic moulding electrical, manufacturers now embed electronic components directly into the plastic parts during the moulding process. This evolution includes the utilization of conductive plastics, integrated wiring, and micro-electronic assemblies to achieve multifunctionality in a single manufacturing step.
Key Technologies Empowering Plastic Moulding Electrical
- Insert Moulding: Incorporates metal or electronic inserts into plastic components during the moulding process.
- Overmoulding: Adds additional layers of plastic or conductive materials over existing parts, enabling complex electrical features.
- Smart Moulds: Utilizes sensors and automation to ensure precision and consistency in electrically integrated mouldings.
- Conductive Plastics: Materials infused with carbon fibers or metallic particles that conduct electricity, allowing for embedded electrical pathways.
- Microelectronic Mouldings: The miniaturization of electronic components within plastic parts for high-density applications.
Advantages of Integrating Electrical Components into Plastic Mouldings
Embedding electrical functionalities directly into plastic moulded parts offers numerous benefits for business operations and product design:
- Cost Efficiency: Reduces assembly steps, minimizing labor and material costs.
- Enhanced Durability: Tight integration ensures resilience against environmental factors such as moisture, dust, and mechanical wear.
- Design Flexibility: Enables complex geometries and multifunctional components that were previously unfeasible.
- Weight Reduction: Consolidates multiple components into a single part, lowering overall product weight.
- Streamlined Supply Chain: Simplifies manufacturing and reduces inventory complexity by consolidating parts.
The Role of Metal Fabricators in Supporting Plastic Moulding Electrical Business
While plastic moulding electrical focuses on integrating electronics into plastics, metal fabricators play a pivotal role in supporting the entire ecosystem of manufacturing. Metal fabricators provide essential components, enclosures, connectors, and structural frameworks that complement plastic parts, enhancing the overall functionality and robustness of finished products.
Synergistic Collaboration between Plastic Moulding Electrical and Metal Fabricators
The collaboration between these sectors involves:
- Designing composite products that unify plastic electrical components with metal parts for improved strength and electrical grounding.
- Manufacturing enclosures and housings that provide EMI shielding and mechanical protection for electronic assemblies.
- Producing precision metal connectors and terminals compatible with plastic moulded parts.
- Developing custom metal frameworks that facilitate complex electrical routing within products.
Investing in Advanced Manufacturing Technologies
To excel in business in plastic moulding electrical and metal fabrications, companies must adopt state-of-the-art manufacturing technologies. These innovations drive quality, efficiency, and sustainability:
- Automated Injection Molding Machines: Ensure precision, repeatability, and high-volume output.
- 3D Printing and Rapid Prototyping: Accelerate product development cycles and validate complex designs before mass production.
- Smart Manufacturing and IoT: Enable real-time monitoring, predictive maintenance, and optimization of manufacturing processes.
- Laser Cutting and Welding: Provide high-precision, clean cuts, and welds on metallic components supporting electrical design needs.
- Surface Treatment Technologies: Ensure corrosion resistance, electrical conductivity, and aesthetic finishes for metal and plastic components alike.
Ensuring Quality and Compliance in Plastic Moulding Electrical & Metal Fabrication
High-quality products require strict adherence to quality standards and regulatory compliance. Companies like DeepMould emphasize quality assurance through:
- ISO Certification: Ensuring processes meet international quality standards.
- Material Testing: Verifying the electrical, mechanical, and chemical properties of plastics and metals used.
- Dimensional Accuracy: Maintaining tight tolerances critical for seamless electrical integration.
- Electrical Safety Standards: Complying with regulations such as UL, CE, and RoHS for electrical safety and environmental impact.
- Traceability Systems: Keeping detailed records of materials and processes for accountability and quality control.
Custom Solutions for Diverse Industry Needs
Every business has unique requirements. Whether developing a compact electronic device, an automotive sensor system, or a healthcare product, personalized plastic moulding electrical solutions are vital. Companies in this field offer:
- Prototyping and R&D Support: Assisting in designing and testing innovative solutions.
- Small to Large Scale Production: Catering to various production volumes with flexibility and scalability.
- Material Selection Assistance: Recommending plastics, metals, and conductive compounds suitable for specific applications.
- Integration Services: Combining plastic moulding with metal fabrication, electronics assembly, and finishing processes.
- After-Sales Support: Offering repair, modification, and ongoing technical assistance.
Why Choose DeepMould for Your Business in Plastic Moulding Electrical & Metal Fabrication?
As a trusted leader in Metal Fabricators and plastic moulding solutions, DeepMould stands out due to:
- Comprehensive Capabilities: From design to mass production, covering plastic moulding electrical components and custom metal fabrication.
- Experienced Engineering Team: Skilled professionals dedicated to innovation and quality assurance.
- State-of-the-Art Facilities: Equipped with advanced machinery and testing labs.
- Sustainable Practices: Commitment to environmentally friendly manufacturing and material recycling.
- Customer-Centric Approach: Prioritizing client needs and providing tailored solutions to meet specific project requirements.
Conclusion: Leading the Future of Manufacturing with Innovation and Quality
The rapid advancement of plastic moulding electrical and metal fabrication technologies is transforming how products are designed, manufactured, and assembled. Forward-thinking businesses recognize the importance of integrating these technologies to stay competitive and meet modern consumer demands for smarter, more durable, and eco-friendly products.
By leveraging expertise and innovative practices, companies like DeepMould continue to drive excellence in the manufacturing industry, ensuring sustainable growth, quality assurance, and customer satisfaction. Whether you need custom electrical integrated plastics, precision metal components, or comprehensive manufacturing solutions, partnering with leaders in the field is essential for success.
Embrace the future of manufacturing—where business in plastic moulding electrical and metal fabrications intersect to create industry-leading, high-performance products that set new standards of innovation and reliability.